Entretien avec Frédéric Le Bronnec, Atlantic Réfrigération Consulting
Selon l’ADEME, la chaleur perdue par l’industrie en France représente un gisement de plus de 100 TWh, donc 60 %, à plus de 100°C. Les principaux secteurs concernés par ces pertes sont la chimie, la plasturgie, le papier, les métaux, mais aussi l’agroalimentaire.
Valoriser cette chaleur perdue représente ainsi un enjeu stratégique pour les IAA, afin d’augmenter les performances énergétiques des sites et des procédés et de réduire leur impact environnemental. D’ailleurs, la majorité des industriels ont déjà mis en place au moins un équipement de récupération de chaleur sur leurs installations de façon ponctuelle. Mais peut ont réalisé un bilan global des puits et sources de chaleur.
Les objectifs de la récupération de chaleur sont les économies d’énergie et la décarbonation. En effet aujourd’hui avec les objectifs de décarbonation de l’industrie, la récupération de chaleur sur groupe froid et la technologie pompe à chaleur deviennent des outils majeurs dans la transition énergétique.
La réalisation de récupération de chaleur ne peut pas s’appuyer seulement sur un bilan thermique des sources disponibles et d’un calcul des CEE correspondant. L’objectif étant l’économie d’énergie, l’investissement (CAPEX) doit se traduire par une baisse des coûts opérationnels (OPEX). C’est pourquoi afin d’atteindre ces objectifs, la conception doit s’appuyer sur une étude méthodologique sérieuse.
Méthodologie – Étude thermique :
- Campagnes de mesures (Débit, Niveau de Température des Utilisations), pour les installations existantes. Cette étape permet de mettre en relief le système existant et de guider dans le choix des solutions potentiels.
- Analyses des résultats (Volume journalier des consommations). Des calculs complémentaires sont nécessaires pour évaluer la capacité de stockage possible en étudiant très précisément les phases d’utilisation et les phases de repos.
- Analyses des systèmes de production d’Énergie (Capacité, et Niveau de température). Cette étape a pour objectif de faire corresponde les sources possibles en fonction des utilisateurs.
- Étude de la variabilité de la réjection en fonction de la température extérieure (hivers/été). Cette étape est très importante et souvent mal appréhendée. En effet une installation de réfrigération à une température de condensation variable en fonction de la température extérieure, et les besoins en réfrigération évoluent aussi avec la température extérieure (les besoins en climatisation des salles de travail peuvent être à 100% l’été et 0% l’hiver). Le bilan de réjection peut varier très fortement d’une saison à une autre, et il convient donc de connaître le talon de l’énergie disponible.
- Analyse par la méthode du pincement « Pinch Analysis » (Étude des niveaux de température des sources disponibles et des utilisateurs).
- Étude d’un concept, évaluation du CAPEX.
- Résultats des gains potentiels, avec calcul de rentabilité sur l’OPEX (Gain énergétique, réduction des couts fixes, aide CEE).
- Prise de décision.
Description technique :
Un système frigorifique est une transformation thermodynamique basé sur le transfert d’énergie. La production de froid est assurée au niveau d’un évaporateur situé dans un système à refroidir : tunnel de surgélation, chambre froide, etc. Un liquide frigorigène, plus froid que le milieu à refroidir, est évaporé dans cet évaporateur. Le fluide suit ensuite un cycle frigorifique avec compression, condensation et détente. Le principe de la récupération de chaleur est de capter cette énergie venant du milieu à refroidir. La récupération se fait sur la condensation.
La condensation peut se décomposer en deux parties : La désurchauffe et la condensation.
La désurchauffe étant la partie de chaleur sensible, représentant de 10% à 12% de l’énergie du condenseur. La condensation la partie de chaleur latente, représentant 80% de l’énergie du condenseur. On distingue aussi une autre source sur le refroidissement d’huile (dans de compresseur à vis).

Il est possible de rehausser le niveau de température de condensation pour une récupération avec une température plus élevée. Pour cela on utilise une pompe à chaleur qui est en fait un système frigorifique en surcompression du système primaire.
La technologie évolue et on peut atteindre des niveaux de température élevés jusqu’à +90°C, voir plus avec des pompes à chaleur hybride +110°C (eau surchauffée).
La récupération se fait avec différents réfrigérants avec des différences liées aux caractéristiques des fluides :
- Plus ou moins de surchauffe.
- Peu ou pas de refroidissement d’huile sur certain.
- Pression plus ou moins élevée.
- Obligation réglementaire pour d’autre.
Rappel des références de fiches pour la récupération de chaleur dans le Programme CEE :
- Système de récupération de chaleur sur compresseur d’air : Fiche IND-UT-103
- Système de récupération de chaleur sur groupe de production de froid : IND-UT-117
- Système de récupération de chaleur sur groupe de production de froid : BAT-TH-139
Retour d’expérience :
Contexte :
Depuis 1970 le site produit de la crème glacée. Ces procédés sont très énergivores, avant la réalisation de la récupération de chaleur et le remplacement de deux chaudières le site produisait l’eau chaude à partir de vapeur.
La réalisation de ce projet en 2017 a permis une réduction de la consommation de gaz de 50%.
Description technique :
Le site est équipé de trois système de réfrigération fonctionnant à l’ammoniac. Une première installation principale type booster (étage basse pression et moyenne pression) pour la production (tunnel de surgélation). Une deuxième installation avec compresseur à vis pour la climatisation de salles et le process (eau glacée) de production en mode indirect eau glycolée à -8/-4°C. Une troisième installation avec compresseur à vis avec économiseur pour la zone de stockage -23°C.
Après une étude basée sur la méthodologie décrite ci-avant, les modifications suivantes ont été réalisées :
- Installation d’un système de récupération de chaleur sur les installations 2 et 3 (Désurchauffeur + condenseur à plaques + refroidissement d’huile). Le talon basé sur le fonctionnement de l’entrepôt permet une récupération pour le chauffage de l’ECS sans impacter la régulation HP flottante permettant de maintenir les performances optimums.
- Un système de stockage 50 m3 pour l’eau chaude sanitaire en adéquation avec les besoins de la production.
- Installation d’une pompe à chaleur sur le système 1. Le chauffage fonctionnant en corrélation avec la production et le niveau de température ne pouvant être atteint avec une récupération sur la désurchauffe et la condensation, une pompe à chaleur à été installée et a permis une économie de gaz importante (sans impacter la condensation de l’installation principale). L’avantage d’une pompe à chaleur est d’associer les besoins chauds à la source de chaleur.
- Remplacement de deux chaudières (2 x 14t/h) par deux chaudières modernes (2 x 3t/h).
- Récupération de chaleur sur le système de compresseur d’air pour venir en complément sur le stockage d’ECS.

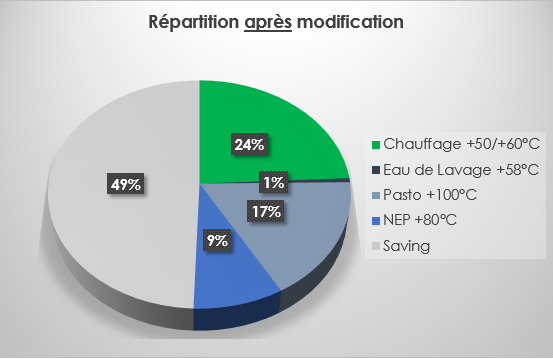
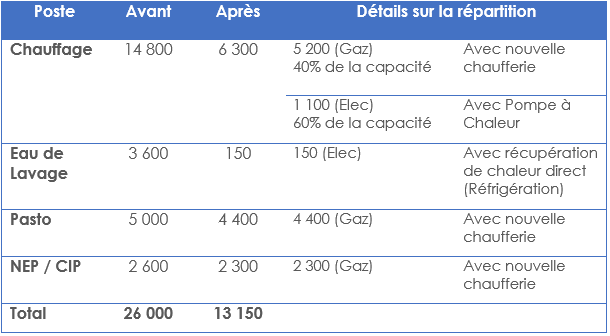
L’installation de la récupération de chaleur et des nouvelles chaudières a permis de réduire de 40% la consommation de gaz, ce qui engendre une réduction des émissions de CO2 de 50% par an.
L’investissement pour l’installation de la récupération de chaleur a été de 2 250 k€, pour des gains 524 k€ par an. Ce projet a bénéficié de mécanismes tels que les CEE. Au final, les différentes aides ont permis de baisser le temps de retour sur investissement à 1,77 ans, rendant viable économiquement le projet.
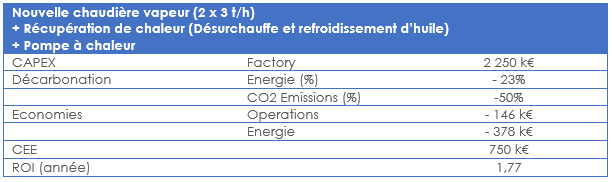
Mécanisme Certificats d’économie d’énergie utilisés :
- Fiche IND-UT-117 : Récupération de chaleur sur groupe de production de froid
- Fiche IND-UT-103 Récupération de chaleur sur compresseur d’air
- Fiche IND-UT-102 Système de variation de vitesse sur moteur asynchrone
- Fiche IND-UT-116 Haute pression flottante
- Fiche IND-UT-104 Économiseur sur chaudière vapeur
- Fiche IND-UT-105 Brûleur micro modulant sur chaudière industrielle
- Fiche-IND-UT-125 traitement d’eau performant sur chaudière vapeur
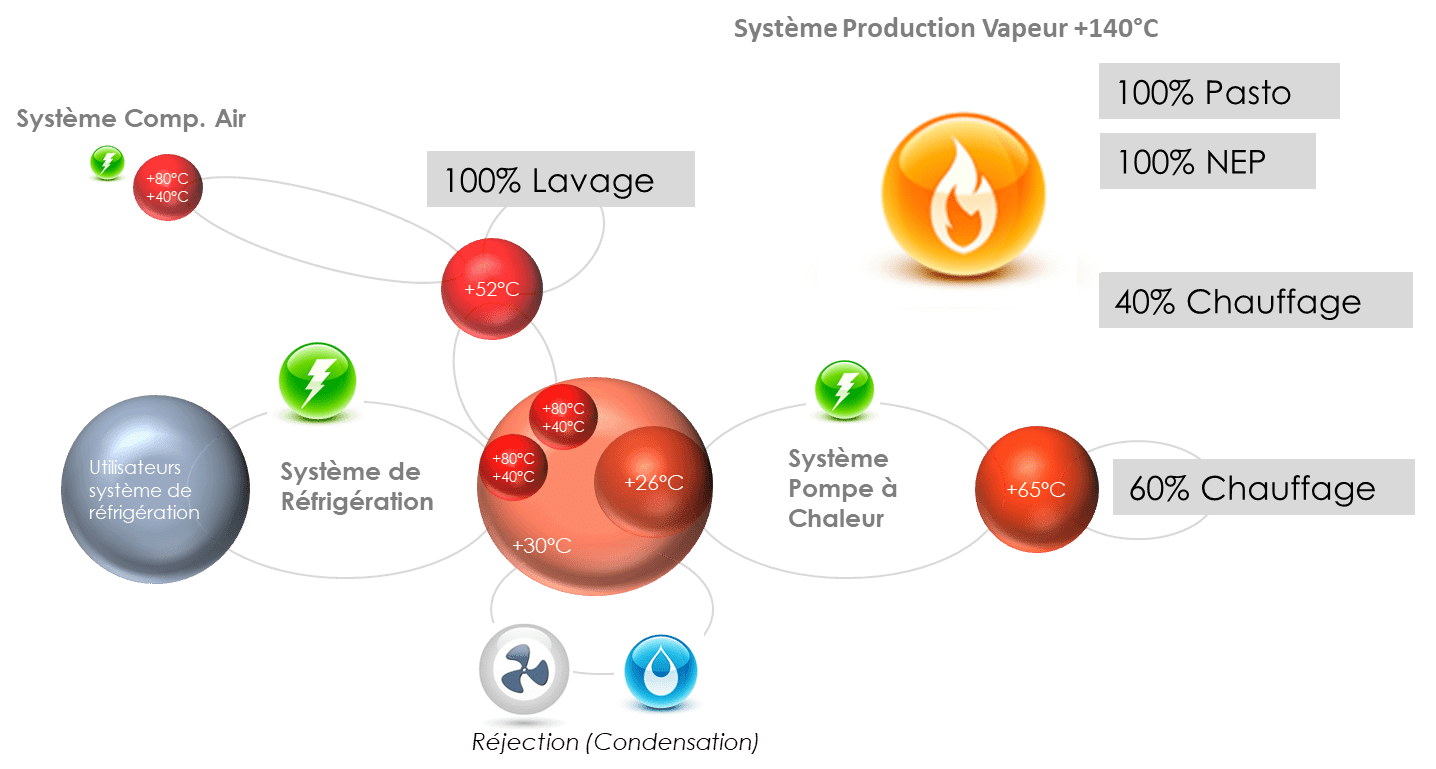
Glossaire :
- CEE : Certificats d’Economie d’Energie
- IAA : Industrie Agroalimentaire
- CAPEX : Capital Expend (Coût d’investissement)
- OPEX : Operational expend (Coûts opérationnels)
- ROI : Retour sur Investissement
- ECS : Eau Chaude Sanitaire
Frédéric Le Bronnec, Atlantic Réfrigération Consulting
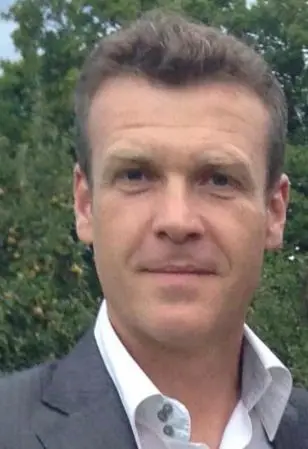